unspun is a mission driven company. We’re developing 3D weaving technology to dramatically slash pollution in the fashion industry. At the same time we’re realists. We acknowledge that good intentions alone won’t achieve our goal. To usher in a future where clothing manufacturing is truly sustainable, 3D weaving has to be cost-effective.
From our recent Life Cycle Assessment (LCA), we know that our Vega™ 3D weaving machines can significantly reduce the environmental impacts of making pairs of pants. The ways our Vega™ machines do that also point to ways in which 3D weaving can save on the costs of making clothes without raising their prices. A sustainable future doesn’t only do right by our Earth. It's a win-win for the bottom line and the pocketbook.
There are several key reasons why 3D weaving is good for business. We can summarize them simply: 3D weaving saves more and wastes less while improving the customer experience. To understand these benefits, we can think of 3D weaving as a manufacturing technology, a business model, and a retail experience.
We’ll analyze each side of this equation in three parts: how 3D weaving as a manufacturing technology decreases production expenses (herein); how as a business model it optimizes inventory (part 2); and how as a retail experience it builds customer trust (part 3).
Without further ado.
Key points
• 3D weaving is a technology that establishes a new, condensed process for making clothes, in which fabric preparation and clothing assembly are combined into one step.
• This new process, called Vega™ manufacturing, incurs fewer expenses to make woven clothes compared to conventional apparel manufacturing.
• Vega™ 3D weaving machines save on costs by automating and speeding up production while using less energy compared to conventional machines.
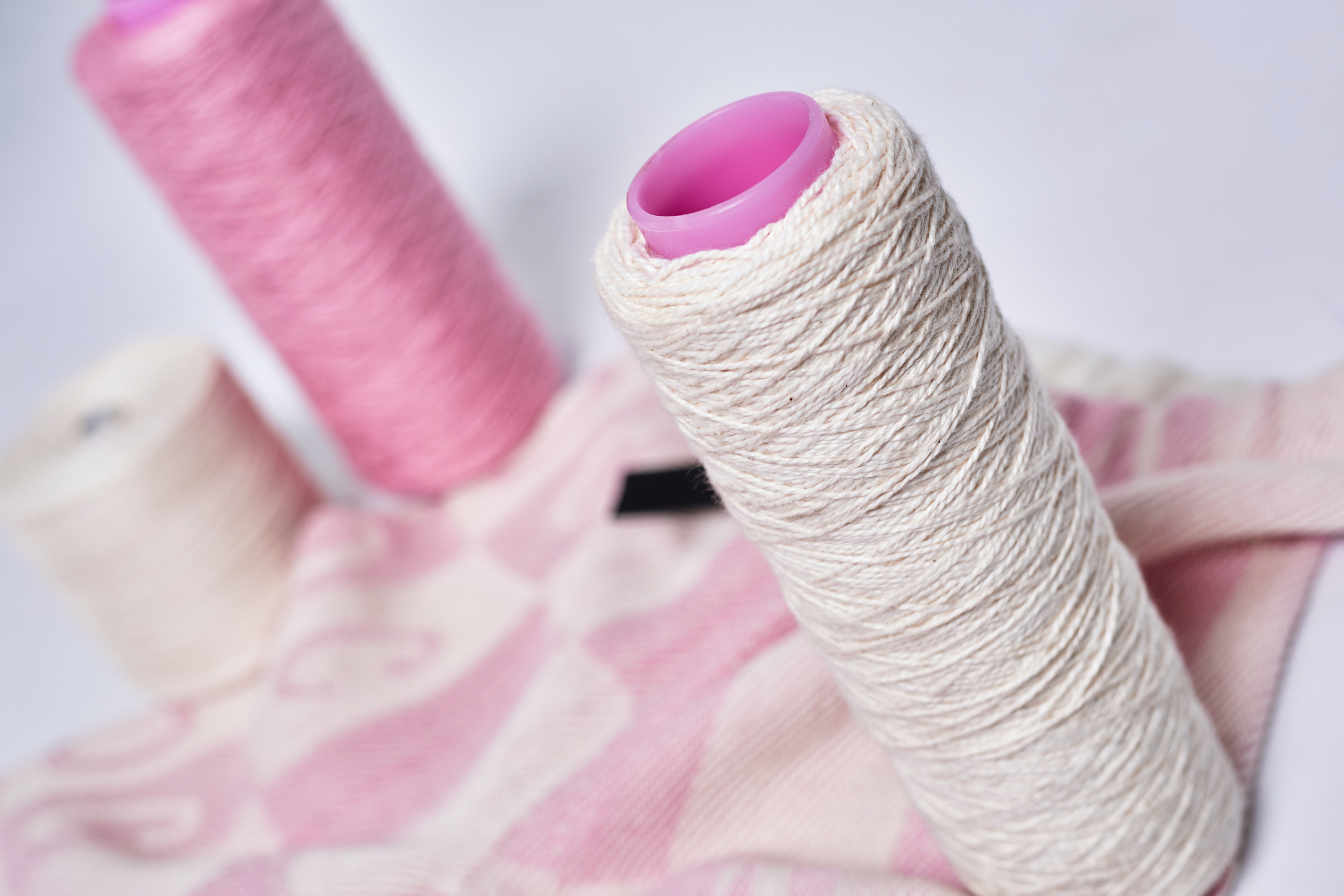
3D weaving as a manufacturing technology
We haven’t changed how we make woven clothes in 200 years. Today, the fashion industry still produces clothing by cutting patterns from rolls of woven fabric as it did at the beginning of the Industrial Revolution.
Over time, manufacturers and fashion brands have lowered the cost of production by reducing the technical inefficiencies and labor costs of this conventional manufacturing process. Using a Vega™ 3D weaving machine takes a different approach. 3D weaving economizes the cost of production by establishing a new manufacturing process altogether.
To better understand our 3D weaving process, consider how clothes are currently made. After fibers have been spun into yarn and before completed garments are washed, broadly speaking, conventional apparel manufacturing occurs in six steps. Those steps are: beam warping, in which warp yarns are wound onto a beam; dyeing and finishing warp yarns (or, once yarns are woven, dyeing and finishing fabric); weaving yarns into a roll of fabric; cutting patterns from that roll of fabric; sewing garments from those patterns; and adding trims.
Executing these six steps requires the operation and maintenance of a lot of machines. Typically, these are located in two separate facilities run by two distinct manufacturers. A fabric mill contains machines for preparing rolls of fabric, such as beaming machines for warping, lift trucks for loading beams, any of various dyeing machines, and air-jet looms for weaving. Elsewhere, a sewing factory contains machines for the last three steps of the conventional process, commonly referred to as Cut, Make, and Trim (CMT). These machines include lasers or industrial saws for cutting as well as an assortment of sewing and trimming machines needed to complete a garment.
3D weaving technology condenses conventional manufacturing into fewer steps. This is no minor innovation. In uniting Tiers 1 and 2 of the fashion industry supply chain, a Vega™ 3D weaving machine streamlines the process of making clothes, while creating new opportunities for vertical integration.
To explain, a Vega™ machine weaves cones of yarn into seamless tubes of fabric. Each tube is a piece of clothing, like a pant leg, that can be dynamically sized in length and width as it is woven.
This mechanical invention alone combines beam warping, weaving, and cutting into one step. Using a Vega™ machine also skips the dyeing and finishing step, for the reason that it weaves with pretreated yarns (alternatively, completed garments may be garment dyed). Finally, the outputs of a Vega™ machine minimize the number of sewing tasks, effectively combining sewing and adding trims into one step.
Consequently, the 3D weaving process occurs in two steps: weaving yarn into tubes of fabric that are pieces of clothing, and attaching those pieces and trims. These two steps require far fewer machines. Those machines, moreover, are housed in a single, space-efficient microfactory run by one manufacturer or fashion brand. Vega™ 3D weaving machines simultaneously prepare fabric and assemble pieces of clothing. On-site, a smaller assortment of machines for sewing and adding trims are on hand to complete a garment. We call this Vega™ manufacturing.
The 3D weaving process is good for business because it conserves resources of all varieties. Saving more of what’s needed to make clothes decreases the cost of every article of clothing.
.jpeg)
3D weaving automates production
While increasingly sophisticated machines have lowered the cost of producing clothing, to the present, automation has only made the steps of conventional apparel manufacturing more efficient. It has not condensed those steps or consolidated the labor needed to complete them. That’s why conventional manufacturing still heavily relies on dozens of machines, even as those machines, and the tasks that dozens of workers perform with them, become more specialized.
In contrast, Vega™ manufacturing demands fewer machines, and fewer workers to operate them, to execute a smaller number of steps. In this circumstance, automation reduces fixed costs, specifically the cost of investing in and maintaining equipment, as well as the cost of leasing or buying factory space to contain that equipment. Automation also calls for a more nimble and skilled workforce, reducing the number of recurring labor costs. These concurrent savings shrink unit costs, or render unit costs more competitive, depending on location.
3D weaving automates many of the tasks in conventional manufacturing in a straightforward manner. Vega™ machines replace those machines needed for beam warping, weaving, and cutting fabric, and one Vega™ technician assumes the roles associated with those steps. Meanwhile, the seamless construction of 3D woven pieces of clothing relieves sewing teams of having to use dedicated machines to stitch side seams. And because it focuses production in one microfactory, Vega™ manufacturing obviates the need to transport rolls of fabric.
Manufacturing trends toward automation. By simplifying clothing manufacturing, 3D weaving technology introduces new ways for manufacturers and fashion brands to spend less on production costs without sacrificing efficiency or resorting to ever cheaper labor. Our technology additionally promises to upskill the workers they employ, better positioning all involved for a global market in which overproduction is disincentivized and regulated.
Unlocking greater value in every article of clothing begins here, with greater automation.
3D weaving speeds up production
Depending on a fashion brand’s business model, a typical garment takes anywhere from several months to just weeks to make. Fast fashion brands are criticized — rightly — for increasing the volume of products and accelerating the speed of production, without lowering the environmental impacts of either. Unequivocally, this way of making clothes is a massive waste. Yet the market incentive for speed is clear: the faster a brand can manufacture clothing, the more adeptly it can respond to demand. However, the same technological impediments that prevent conventional manufacturing from automating its many tasks prevent it from making clothes at maximal speed.
Vega™ 3D weaving machines attain that speed. Combining beam warping, weaving, and cutting into one manufacturing step, 3D weaving exponentially condenses the time it takes to make clothes. This speed doesn't merely save time on the factory floor. It can bring the moment of production even closer to the time of sale.
By way of example, consider a single pair of pants. A Vega™ 3D weaving machine can weave two pant legs in 10 minutes total. In 10 more minutes (for now, in keeping with the industry average), our in-house sewing team can attach each leg and trims.
This is the fastest method of weaving and assembling clothes of which we're aware. What is more, time saved at the point of production shortens the time to market: once a pair of 3D woven pants is designed in a matter of days, it can be produced in a matter of minutes.
For perspective, in the time it takes to make five pairs of pants using our 3D weaving process, a comparably automated circular knitting machine can make one pair, using more yarn in a less durable construction. Even then, knitting machines cannot bring down the time to market for any woven article of clothing. Under the conventional process, fast fashion manufacturers can design and produce a garment in 10 days at peak speed.
The manner in which saved time saves on production costs is difficult to quantify: the materials, labor, and energy not spent to manufacture clothing is best measured by the manufacturer or fashion brand enjoying the savings. Nonetheless, the principle benefit is easy to grasp. In a word, Vega™ manufacturing empowers fashion brands to make clothes in a manner more closely aligned with demand, as determined by real time sales analytics.
Responding to demand, rather than predicting it, lowers the likelihood that brands will overproduce inventory, while removing the need for demand forecasting garment sales in the first place. As a bonus, spending time producing only what will sell, or has already sold, frees up more time for product research and development.
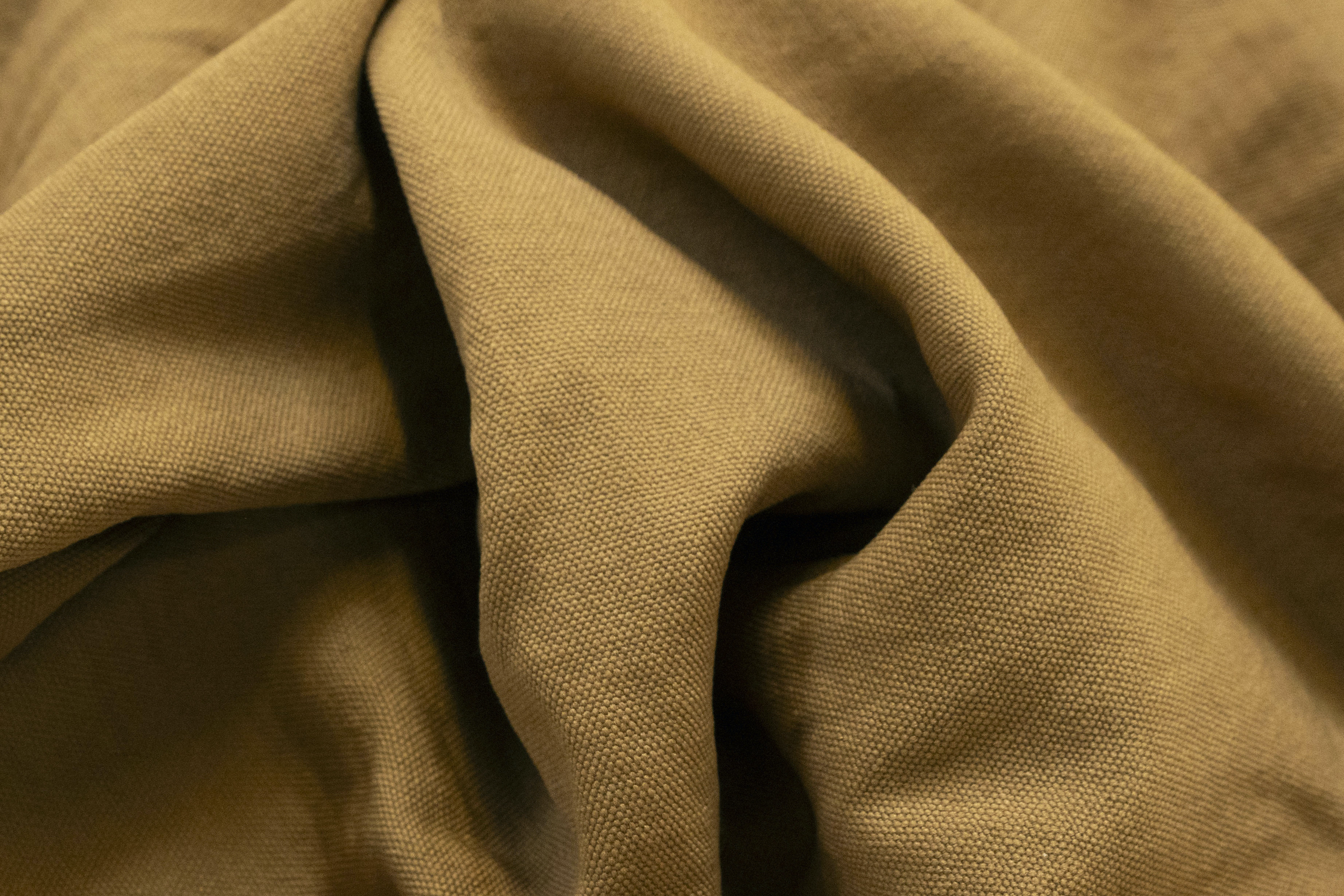
3D weaving uses less energy
Making clothes, and particularly weaving fabric, is energy intensive. In the life cycle of a pair of jeans, for instance, the aforementioned six steps of conventional manufacturing are responsible for about one third of its greenhouse gas emissions. Yet fuel and electricity consumption isn’t limited to manufacturing alone. Fiber cultivation and transportation contribute to energy demand. So too does the amount of fabric used to make a garment. Ultimately, these variables affect the cost of production.
Even with precise machines, weaving rolls of fabric and cutting patterns from them creates excess scraps. On average, 16.5% of fabric becomes waste during the weaving and cutting steps, according to Phase 2 of our LCA. That waste isn’t sold, but instead is landfilled, incinerated, or woven again only after recycling. It represents energy that doesn’t lead to profit.
In the same manner that it demands fewer machines, 3D weaving demands less energy for production. Accounting for energy expended throughout the fashion industry supply chain, Vega™ manufacturing uses 25% less energy than conventional manufacturing, according to Phase 1 of our LCA.
These savings are both direct and indirect. At the point of production, a Vega™ 3D weaving machine outright needs less power to operate than an air-jet loom. A Vega™ machine also operates more effectively, such that a mere 3% of fabric becomes waste when making a 3D woven garment. Producing that garment with less yarn than would be used in the conventional process conserves energy in Tiers 3 and 4 of the supply chain. Furthermore, just as focusing production in one microfactory obviates the need to transport of rolls of fabric, it obviates the need to burn fuel for transportation as well.
By expending less energy, Vega™ manufacturing can limit the overhead of manufacturers or fashion brands, and extract more value from raw materials. To compound those savings, decreasing energy use may also insulate factories against fluctuating energy prices, and better utilize cheap energy generated on-site from renewable sources. Regardless, decreased use outperforms any future energy savings today's manufacturers might hope to realize: since the efficiency of lasers and industrial saws has plateaued already, the weaving and cutting steps of conventional manufacturing will continue to output excess scraps indefinitely.
The real-world advantages of 3D weaving
The savings afforded by the 3D weaving process are unique to Vega™ 3D weaving machines. They are not an add-on to, or a hack for, conventional manufacturing; they’re a built-in advantage of using Vega™ manufacturing to unite Tiers 1 and 2 of the fashion supply chain.
In recent years, the costs of equipment, labor, materials, and energy have climbed in manufacturing hubs across the world. Unforeseen market shocks caused by extreme weather events, geopolitical developments, and sudden changes in customer demand have tested the resiliency of the fashion industry as a whole.
To maintain edge in the market today, we believe manufacturers and fashion brands must do more than lower the sum of expenses in their supply chains. They must incur fewer expenses to begin with. They must gain greater value from the clothes they make by saving more on production costs, and by exploring vertical integration.
Vega™ 3D weaving machines herald this future of saving more. By disrupting conventional apparel manufacturing through automation, speed, and energy efficiency, Vega™ manufacturing promises to strengthen the competitiveness of forward-thinking manufacturers and fashion brands.
That’s one reason why Vega™ is good for business. Although, remarkably, it’s not actually the most important one. Saving more is simply the basis for wasting less.
Read on in part 2 (forthcoming).
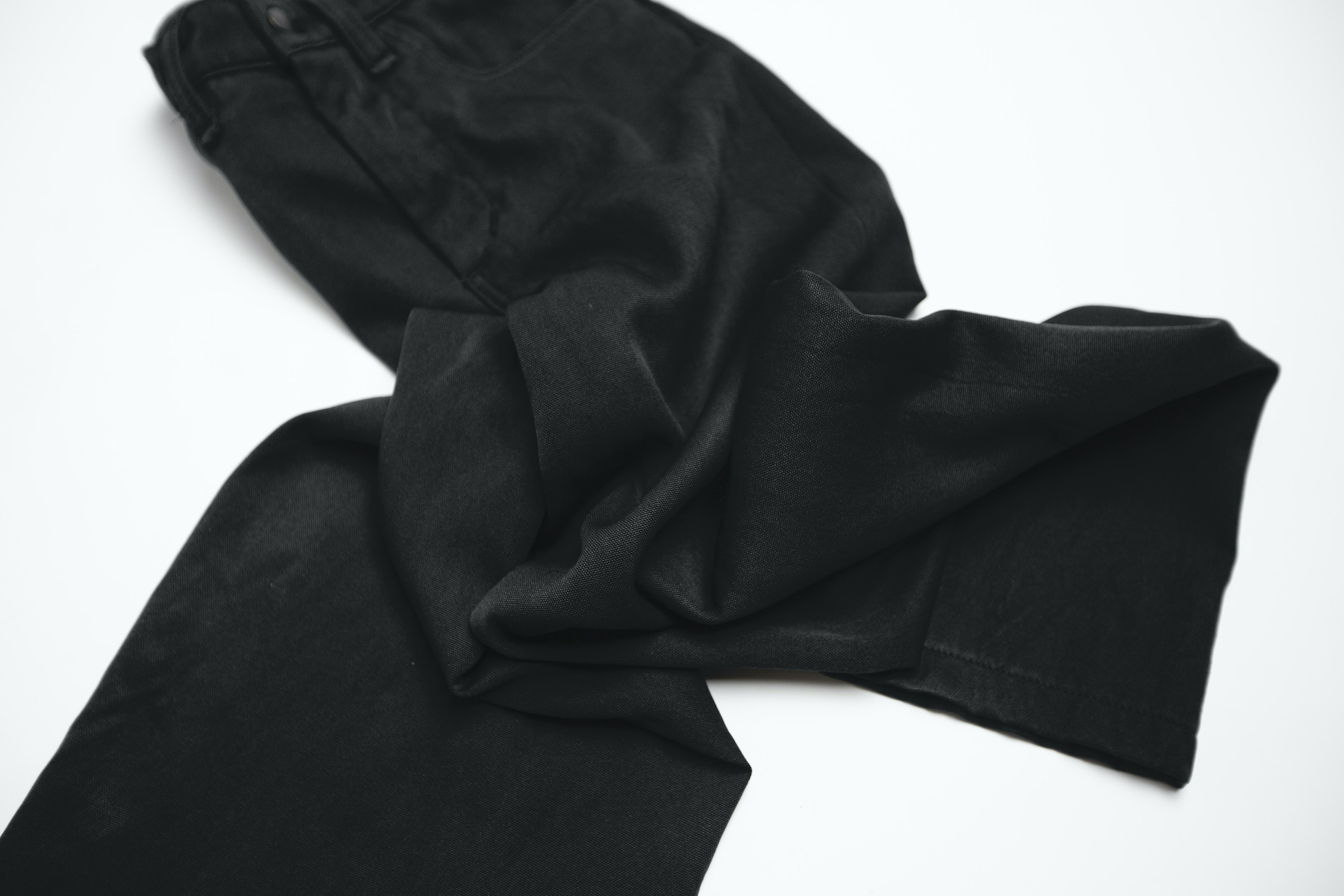